When Continuous Flow Won't Work: Implementing Pull Systems In Medical Device Manufacturing
By Darren Dolcemascolo, senior partner and co-founder, EMS Consulting Group
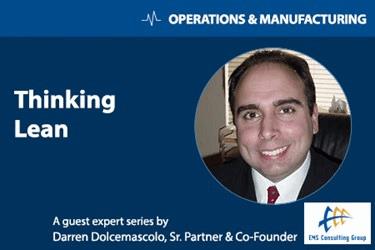
In our previous Thinking Lean series discussion, we talked about methods for creating continuous flow. Continuous flow is the least wasteful method of connecting processes within a lean value stream. In this edition of Thinking Lean, we will talk about pull systems, which should be utilized in cases where continuous flow is not feasible.
In many cases, when designing lean value streams, there are processes that do not lend themselves to continuous flow. For continuous flow to work, processes need to be reliable and repeatable. They also need to be able to be scaled to takt time — the rate at which the value stream needs to produce to meet customer demand.
For example, processes such as injection molding, metal stamping, and heat treating often cannot be scaled to run at takt time. Metal stamping and injection molding processes often run faster than takt time, and heat treating often runs much more slowly than takt time. These processes usually have long changeover times. Thus, they are batch-and-queue processes by design. How does the lean manufacturer control production for such processes?
Type A Pull System (Replenishment Pull)
While the mass producer controls production using a traditional push system, in which each manufacturing area is scheduled independently based on a material requirements planning (MRP) forecast, the lean producer uses a pull system. That is, the batch-and-queue processes will replenish a supermarket of parts, which will be consumed by a downstream, one-piece flow process (such as final assembly).
The downstream process withdraws parts from the supermarket. As parts are consumed and a trigger point for replenishment is reached, an order is then sent to the upstream batch process, which runs a batch of product to replenish the supermarket. Below is an illustration of a plastic injection molding process replenishing a supermarket of plastic parts from which two one-piece flow cells withdraw parts. This is called a supermarket pull system, or simply a “Type A” pull system.
On the right side of the illustration, we see a workcell. A work-in-progress (WIP) supermarket contains parts that are supplied to the workcell. As the parts are consumed by the cell, a signal kanban (represented here by the triangle) is sent to the supplying process, which will replenish the parts to the supermarket. Parts will not be overproduced, since production of the parts is based only on downstream consumption.
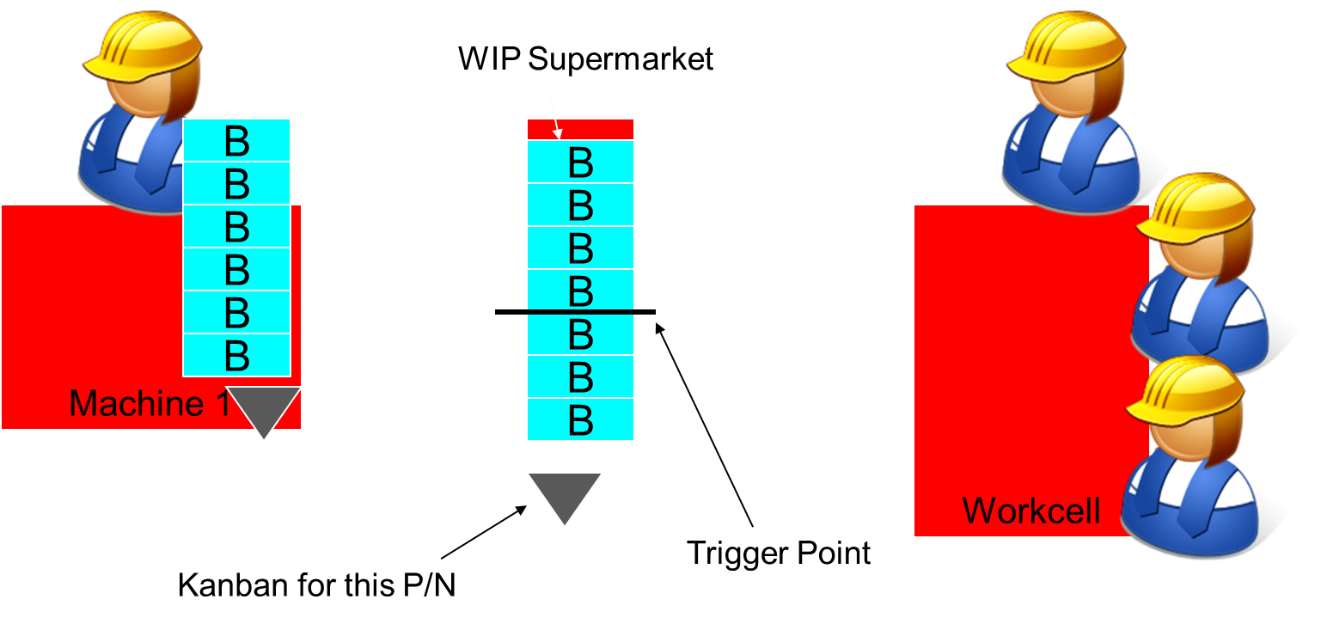
In order to implement this type of system, we need to understand the demand or consumption rates downstream, the variability of both demand and supply, and the frequency of replenishment. This will allow us to calculate how much inventory we need to keep in the supermarket and to determine the trigger point — the point at which we send a signal, or kanban, to the supplying process for replenishment.
Type B Pull System (FIFO Lane)
A replenishment pull system is not always the solution for production control within a lean producer's value stream. While replenishment pull systems work well in many cases, for high mix or job shop environments, such pull systems are rarely the right solution. Consider a job shop whose customers are ordering one-of-a-kind products in low volumes. Customization would make supermarkets impractical for controlling inventory between processes.
Instead, an alternative, such as a first in / first out (FIFO) lane, also called a sequential pull, might be implemented. A FIFO lane is a buffer that can be used to hold a certain amount of inventory between an upstream (supplying) and downstream (consuming) process. Unlike a supermarket, it does not hold a certain quantity of particular inventory; it holds a certain quantity of total inventory. Items are pulled in sequence from the FIFO lane. When the lane is full, the supplying process stops producing parts. A FIFO lane is sometimes an actual lane on a factory floor, in which parts can accumulate.
In the illustration below, we see a FIFO lane between two workstations. Workstation 1 produces product into the FIFO lane, which allows a maximum of 5 units. Workstation 2 pulls from the FIFO lane in first-in / first-out sequence. If the FIFO lane becomes full, this is a visual signal, and action must be taken. Typically, workstation 1 would stop producing with a full FIFO lane. In some cases, additional action might be taken. For example, additional resources might be sent to workstation 2 if the FIFO lane becomes full.
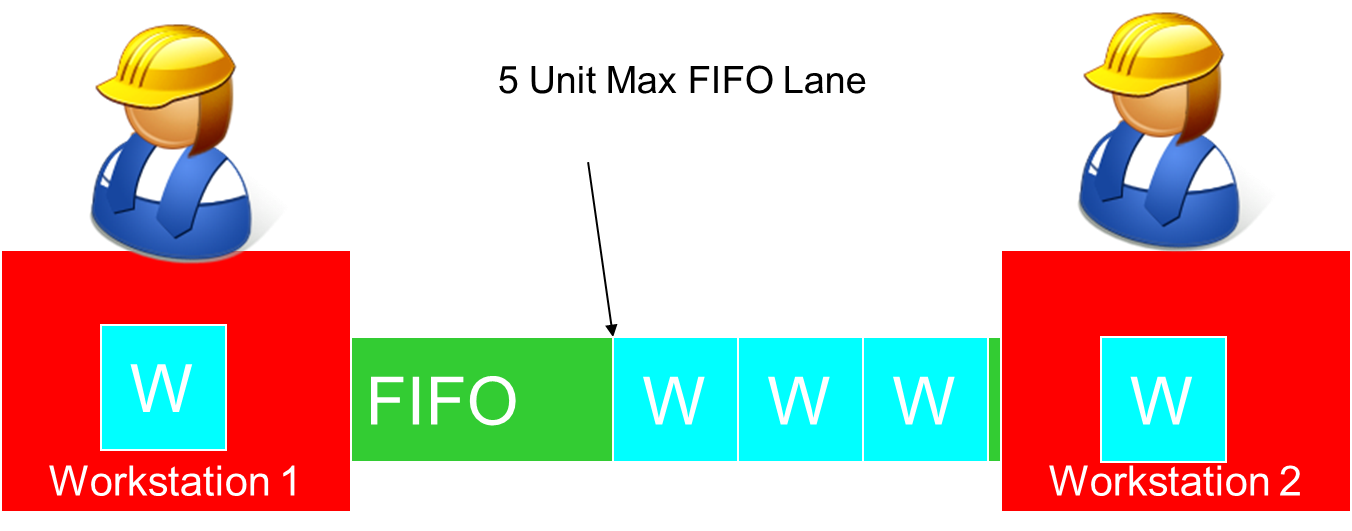
Example: Pull System At A Medical Device Manufacturer
Let’s discuss application. This is a case study in which a medical device manufacturer implemented replenishment pull between an injection molding operation and two assembly cells.
The company had 12 plastic injection molding machines. Each produced a number of components that were assembled into a finished product by the assembly cells. Before the implementation, the company had about 10 days of injection molded inventory (WIP). There were also a significant number of material shortages affecting the productivity of the assembly cells.
A kaizen team — consisting of a materials person, assembly and injection molding operators, an industrial engineer, an area supervisor, and a few employees from outside the area — was formed. After spending day one in training and mapping out the current state process, the team discovered significant waste in the process:
- Daily material shortages were resulting in significant overtime costs/reprioritization.
- Inefficient planning for changeovers in the injection molding department occurred due to shifting schedule/priorities.
- Out-of-cycle work: Operators were doing their own material handling and preparation.
- Excessive WIP (10 days)
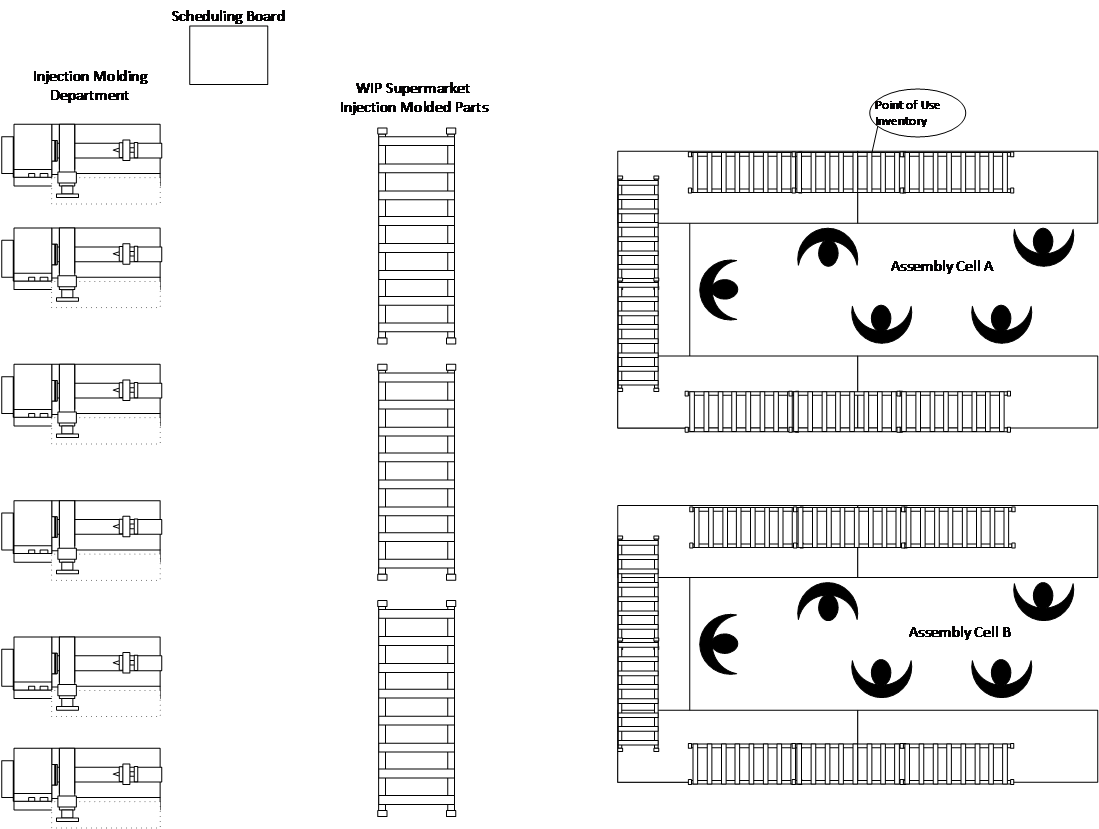
After analyzing material usage and variability in usage, the team created and properly sized a supermarket of plastic materials. The system, represented in the layout above, worked as follows:
- Material handlers would pull from the supermarket into the assembly cells, replenishing point-of-use inventory using a two-bin system. That is, as bins of plastic parts were emptied, the empty bin was used as a signal to replenish material to the cells.
- As materials in the supermarket were consumed (moved into assembly), a trigger point (visually indicated by the number of bins remaining) was reached. When the trigger point was reached, a kanban card would be pulled and delivered to the injection molding lead.
- The injection molding lead would place the kanban on a scheduling board in sequence.
- The injection molding machines would run product according to the kanban on the scheduling board and replenish the supermarket.
The new system resulted in a 90 percent reduction in shortages and a 70 percent reduction in WIP (from 10 days to 3 days).
In conclusion, pull systems are an essential part of lean production system; it is very rare that any organization can be pure continuous flow. In cases where continuous flow is not feasible, organizations should adopt a type A and/or B pull system. Pull systems prevent overproduction as well as shortages, and result in inventory reductions and shorter production lead-times.