Liquid Silicone Rubber Injection Molding
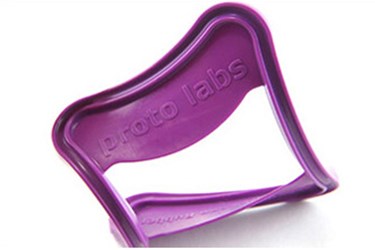
Liquid silicone rubber (LSR) molding is a thermoset process that mixes a two-component compound together, which is then heat cured in the mold with a platinum catalyst to produce a final part. Liquid Silicon Rubber parts are formed through an injection-molding process similar to that of conventional plastic injection molding with one major difference — the material delivery system is cooled and the mold is heated. Liquid silicone rubber possesses thermal, chemical and electrical resistance, plus biocompatibility. Also, Liquid Silicone Rubber parts can withstand sterilization while maintaining physical properties at extreme temperatures.
Proto Labs brings a practical and cost effective way to get real liquid silicone rubber parts, really fast. They use Protomold technology to analyze part geometry, provide design and manufacturability feedback, and produce the tools. At Proto Labs, their Liquid Silicone Rubber injection molding process is suitable for producing low volumes of liquid silicone rubber parts — typically between 25 to 5,000+ pieces, but up to 25,000 in some cases — in about three weeks from order to delivery of samples. Depending on part complexity, it is possible to get parts faster. Standard expedite offerings and rates apply on eligible parts. The equipment and processes that they use are directly in alignment with industry standards, so a transition to high volume is seamless.
Proto Labs stocks a tange of LSR materials that are suitable for various part applications and industries. Choose from standard silicones in multiple durometers along with optical, medical, and fuel-resistant grades.
Contact Proto Labs to discuss how their liquid silicone rubber injection molding services can be utilized in your next design. Visit their website for more information.