3D Printing Custom-Fit Stents
By Chuck Seegert, Ph.D.
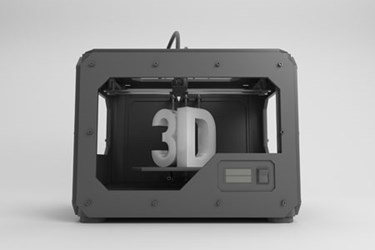
The trend for personalized implants has recently advanced with the development of 3D printed, custom stents. These additively manufactured medical devices are generated using medical-grade silicones and hold airways open with a closely matched fit that greatly outperforms off-the-shelf devices.
The value of 3D printing has become more apparent as today’s healthcare environment shifts toward personalized solutions. Custom implants have come to the forefront, and 3D printing has been used to fabricate spinal implants, craniofacial implants, and much more.
Now, this versatile and rapid method of manufacturing has found an application that remedies collapsed airways, according to a story from the Boston Globe. The idea originated when Dr. George Cheng, a research fellow at Beth Israel Deaconess Medical Center, read an article in the New England Journal of Medicine. The article discussed a boy who was treated with a tracheal splint made by a 3D printer, which prompted Cheng to wonder how stents could be improved.
“We think that by 3-D printing, we can make the perfect-size stent for the patient,” said Adnan Majid, an assistant professor of medicine at Harvard Medical School and a pulmonary specialist at Beth Israel who has served as Cheng’s adviser on the research, according to the Boston Globe. “It may be faster, cheaper, and ultimately translate into better patient care.”
As healthcare turns toward more effective and lower-cost options, the idea of personalized medicine has been gaining momentum. Something designed for a specific patient that can be made cheaply promises to improve outcomes on an individual basis. The FDA has closely followed this issue and has even gone so far as to develop recommendations on how to approach it.
In the case of airway stents, the 3D printed version fits the contours of the trachea perfectly, according to the Boston Globe story. This improves the performance of the device by preventing the device from sliding around like off-the-shelf stents. In this particular case, the device itself wasn’t printed — instead, a mold was created with the printer that allowed the silicone to be polymerized inside it.
As personalized medicine continues to rise in prominence, a number of hurdles may need to be overcome from regulatory and business standpoints. Overall, however, the future of this manufacturing method is certainly bright.