An Introduction To Emerging Polymers For Medical Devices
By Len Czuba, President, Czuba Enterprises, Inc.
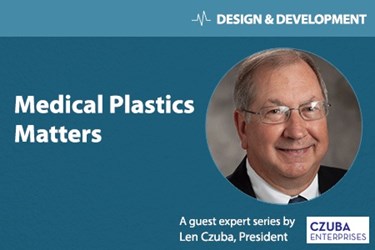
I spend a great deal of time with engineers who are working on new medical devices. They often need help selecting the best material for the parts and devices they are developing, a polymer that will make their new product functional and safe. But more frequently the focus is on how much will the material cost and what will be the final cost of the device?
Depending on the type of device they are producing, the importance of material cost varies. For high-volume, single-use, devices, the material cost is of greater importance than in a reusable device or most implanted materials. Additionally, when the device being developed has unique requirements, developers must consider what material will have the necessary physical, chemical and biological properties that will allow its use at the lowest possible cost.
So my work in selecting a material often starts with a series of questions:
- Cost — “How much will you use in a year” and “What are you willing to pay for this material?”
- Physical properties — “What are the requirements for the material and/or the part made from our selected polymer?” “How will the part be produced from the material?” “Will it be injection molded, extruded or machined?” “What will the component or the device need to do in its final form?” “Will it need mechanical strength?” “Will it need to resist breakage and when exposed to forces during use?” “Does the device or this component need to be transparent or will an opaque material be satisfactory?” “How flexible or stiff does this material and the parts made from it need to be?”
- Chemical and biologicals properties — “Will it be exposed to chemicals during assembly (solvent bonding) or in use (disinfectants or cleaners)?” “Will it have any contact with the human body; skin, tissue, blood?” “How will it be sterilized?”
- Regulatory concerns — “Has the material been used before in other FDA-cleared devices or approved by foreign regulatory bodies for use in other parts of the world?”
With answers to these questions and, usually, many others that will come up during development, the engineers and development teams can, in a relatively short time, come up with candidate materials.
Some of the newer materials on my watch list include:
- Ketone polymers – Polyether ether ketone (PEEK) and some of its copolymer forms
- Polyethylene and cyclic olefin copolymers (COCs) – Specifically ethylene vinyl acetate (EVA)
- Bioresorbables – Polylactic acid (PLA), polyglycolic acid (PGA), Polycaprolactone (PCL) and the various copolymers that can be made by combining these and other starting ingredients
- Fluoropolymers – Specifically, polytetrafluoroethylene (PTFE), perfluoroether (PFA) and fluorinated ethylene propylene (FEP)
Most of these materials have been around for a long time but their suitability for use in medical devices is only now being recognized and put to use.
PEEK Polymers
When PEEK polymers were first introduced, their high heat resistance, coupled with their remarkable inertness, made them an ideal material for applications that placed a device in contact with tissue and blood. PEEK polymers are not affected by most solvents, lipids or blood, and are completely unaffected by enzymes in the body. These properties make them ideal materials for long-term orthopedic implant applications such as bone screws, plates and pins, tissue anchors and suture screws.
More recently, PEEK has been used to replace metal as a hip stem component. As a metal replacement, the ketone polymers more closely match the flexibility of the native bone, especially when compared to steel or titanium hip replacement stems. That flexibility is vital as the bone into which the hip stem is placed tends to flex; a metal hip stem does not flex, resulting in its loosening over time, while PEEK components are not afflicted by this trait.
Although the PEEK polymers have been available for almost 25 years, it is only in the last 10 years that PEEK has been widely accepted for long-term, in-body applications. One of the reasons for its slow growth is that it is extremely expensive and has been subject to limited availability. Invibio has been the recognized supplier of PEEK since it first appeared in the market. But more recently Solvay and Evonik have emerged as suppliers of this specialty material. I am happy to see that there are more suppliers of such a unique material and expect that, with competition, the cost of the polymer may even moderate from its current pricing.
Polyethylene And Cyclic Olefin Copolymers
Polyolefin copolymers such as EVA and COCs offer new options for products traditionally made from other materials. For only a slight cost increase, EVAs offer many advantages. For example, the flexible grades do not have, nor do they need, plasticizers. Likewise, COCs are a remarkable material spanning a range of flexibility, at a reasonable cost. COCs can be used for containers, replacing glass or polyester and they are inherently cleaner, very clear and solvent resistant.
However, neither EVA nor COCs are readily solvent bondable so assembly to tubing or other polymers - as connectors for fluid administration sets, for example – likely would need to be done with either cyanoacrylates or UV light-cured adhesives. These adhesives are readily available from Dymax, Permabond, Loctite and others. EVA polymers are available from a number of suppliers including Celanese, Mitsubishi and LyondellBasel. COCs are supplied by Topas and others.
Bioresorbables
One of the most exciting areas of new material development in the device community is bioresorbables. One of the first to be investigated has been PLA. As a suture material, PLA will maintain its strength until the liquids with which it is in contact begin the dissolution process, eventually leading to the PLA’s complete elimination from the body.
The other bioresorbables are polyglycolic acid (PGL), polycaprolactone (PCL) and several other copolymers. Together, they offer the medical device community a material that can perform a number of different applications. These materials, too, can be used as bone screws, small orthopedic plates or rods but they typically do not have the physical properties needed for any high-stress applications (e.g., bone reconstruction).
However, these materials are idea when used as tissue anchors, vascular stents or internal meshes that allow cell seeding and reconstruction of an organ as in repairing a perforated heart. Tissue and organ scaffolding are some of the most recent applications well-suited to these unique materials. Another possible area of increasing use will be drug delivery. These applications comprise some of the most exciting opportunities in the area of medical polymers.
Current suppliers of the bioresorbables include Purac and Boehringer Ingelheim.
Fluoropolymers
Fluoropolymers are wonderful materials that come in many combinations and in many different forms. Most everyone knows about the common fluoropolymer, polytetrafluoroethylene (PTFE) originally marketed by DuPont with the tradename Teflon. In the medical device industry PTFE in its solid form can be used for in-body applications because it is very clean and inert in blood or tissue. But the material is very soft and is not useful for any load-bearing applications.
In forms other than solid, PTFE can be made into porous membranes or rods or tapes. These membranes can be used as filters, non-fouling surfaces or hydrophobic surfaces. Other forms of the fluoropolymer such as perfluoroether (PFA) and fluorinated ethylene propylene (FEP) polymers are melt processable by either extrusion or injection molding. Although the materials are difficult to process, products made from them have interesting properties such as inherently non-stick surfaces, high gas barrier properties and in some, transparency.
Suppliers of these polymers for the medical device industry are Daikin Americas, 3M Corp.and W.L.Gore & Associates.
Other Promising Materials
Among the emerging materials of interest are a few traditional, or legacy materials that are being redesigned to improve their properties for specific applications: These include polyesters, urethanes and improved thermoplastic elastomers (TPEs). TPEs are compounds based on polyolefin technology.
For both polyesters and polyurethanes, the breadth of material properties is dependent on the chemistry used to produce the polymer. Polyesters can be made rigid for bottles and containers, like the widely used polyethylene terephthalate (PET) polymer or made flexible with properties that closely match flexible polyvinyl chloride (PVC). The ability to engineer polyurethane polymers to a wide spectrum of properties allows them to be considered for almost any application. They can be soft enough to replace PVC in tubing or sheeting, or to serve as a soft gel-like wound covering, or they can be extremely rigid, like wheels or bumpers on carts.
Both the polyesters and the polyurethanes offer many of the properties common to some of the more widely used polymers, but at a significant cost penalty – two, three or even four times the cost of the polyolefins or flexible polyvinyl chlorides now being used. Suppliers of polyesters for the medical device market include Eastman and DAK, while polyurethanes are available from DSM (formerly known as PTG) or Lubrizol (formerly known as Thermedics).
The Right Material Requires The Proper Manufacturing Technique
The combination of one or more of these newer, non-traditional polymers coupled with evolving manufacturing methods opens new pathways for sophisticated medical devices. Researchers are working on dissolvable sensors with electrically conductive circuits which function in tissue or the bloodstream for a predetermined period of time before being absorbed into the host tissue and then are eliminated from the body via its normal processes.
Some exciting new processing technologies are also helping change the landscape of new product development. The ability of additive manufacturing to produce functional parts with some of the high-temperature materials such as PEEK or polyphenylsulfone (PPSU) for long-term implantable components is just one such enabling technology. Another additive manufacturing process allows multiple materials, with different colors or different stiffness to be combined into a single part. A third additive manufacturing application takes advantage of high temperature materials making possible new mold-making methods that can incorporate features like conformal cooling in the mold as it is being made. Traditional cooling requires adding cooling channels to a mold after it is made, often resulting in significant temperature differences in non-cooled areas of the mold. The additive manufacturing process also can be used with high-temperature polymers to quickly make entire prototype molds, similar to metal molds, usable for producing limited-run injection-molded thermoplastic parts!
Other new processes that are giving extended properties to molded parts include the powdered metal and powdered ceramics injection-molding processes. By combining these manufacturing techniques with the newest materials technologies, manufacturers can create higher-temperature components that are often more resistant to wear, are more resistant to adverse chemical exposure and are usable in high-temperature environments.
Non-stick surface technology developed at MIT, and now commercially available from LiquiGlide is made possible by engineering the surfaces in a way that prevents even viscous liquids from adhering to the wall of containers. A similar effect is obtained using a fluoropolymer additive from Daikin America. The additive is used with polymers used to create bottles or other containers for high-value contents such as specialty biopharmaceuticals, (e.g., Botox and similar very expensive fluids) where any residual product in the container is the equivalent of losing hundreds or thousands of dollars of product. This same additive may have applications in medical devices that could benefit from a non-stick or anti-adhering surface, for example, non-fouling catheters to resist thrombus formation or other surface build-up.
Conclusions
There are so many exciting new materials and processing techniques that, alone or in combination, will enable the healthcare industry to create innovative, next-generation products. They will allow more effective treatments and the promise of better patient outcomes.
About The Author
Len Czuba is the president of Czuba Enterprises, Inc., whose new product development initiatives include taking medical devices from concept to market. Czuba has a BS in biosciences from Southern Illinois University, as well as more than 30 years of experience in polymer synthesis, compounding and material development in the medical device industry. He may be contacted at LCzuba@czubaenterprises.com, or by visiting www.czubaenterprises.com.